Knowing how to choose the right pipe material is essential when you are shopping for pipes so you won’t end up with a leak and a flood in your own bathroom after only a couple of weeks since you first bought and had the pipes installed. If there is a type of material that you can look into, high-density polyethylene is one good example.
Also known as HDPE, its immense strength, flexibility, long lifespan and high resistance to corrosion, pressure and chemicals are the properties that make itself a worthy material for resilient pipes. HDPE pipes are commonly used in various applications such as mining, irrigation, waterworks, sewage, gas and fire systems. Companies that specialize in gas and water transfer also use these pipes as their preference.
Properties
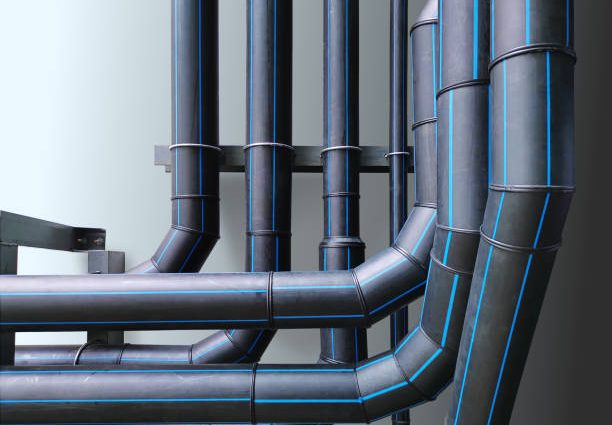
Polythene is the key behind the superior properties of a HDPE pipe. The pipes themselves aren’t the only products that are made of thermoplastic polymer, as it is also used to make various other objects including plastic bags, toys, containers, cutting boards, prosthetics and even plastic surgery, specifically for skeletal and facial reconstruction.
This is made possible thanks to its moldable structure, which can be achieved from its rigid stage by being heated in very high temperatures until it reaches its boiling point.
Polythene also boasts a high strength to density radio, which explains its natural immense strength. The ratio is higher than its sibling, low density polyethylene, or LDPE for short. When looked under a microscope, the structure of the HD polythene is linear enough to leave little branching, resulting in a stronger intermolecular force and tensile strength than LDPE.
Besides its durability, HDPE is also lightweight and it is possible to replace heavier materials with itself to pave the way for sustainable and affordable projects. HDPE is also eco-friendly as it is easily recyclable. It can be recognized on the label of recyclable materials as a recycle logo with the number two on the center.
Downsides
Despite its positive properties, HDPE pipes are not without their shortcomings. To start with, it can crack under stress, though not as much as LDPE. It also has little to no UV resistance, which upon high exposure, may affect its highly valued properties through the degradation of strength and resistance. LDPE shares this similar drawback, although likely with more repercussions as it is weak to extreme high or low temperatures.
One way to prevent further UV exposure and damage on HDPE pipes is installing them indoors or under any roof that shields the sun. Carbon black is also another great alternative, as when used as a resin in the process of molding polythene objects, it acts as an absorber of UV light. The light will eventually dissipate after being turned to heat throughout the objects.
Moving on, polythene can also risk what is known as mold shrinking, in which the volume of a plastic decreases when it gradually becomes cooler and solidifies. This renders bigger objects useless to be created as during the process, the mould remains hot in higher temperatures after the polythene reaches its boiling point.